When assembling your dock on shore, try to do as much of the work as possible without getting into the water. This will make the installation go a lot smoother. Always use hot-dipped galvanized fasteners. Regular, non-coated screws and nails will rust as soon as they get wet.
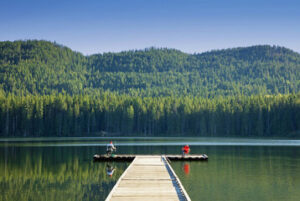
Experts at Mountain Island Lake Dock Builder will reduce your install time, minimize disruption to your property, and deliver a superior end result.
Floating dock kits are increasingly popular as they provide homeowners and marinas with the opportunity to create functional and attractive waterfront structures without the high cost and difficulty of traditional construction. These modular, customizable dock systems can be constructed to suit a wide range of applications, from small waterfront areas to extensive marina complexes. While most floating docks feature a similar design, the choice of accessories and materials can greatly enhance their functionality and aesthetic.
As a general rule, it’s best to assemble as much of the structure as possible on land before moving it into the water. This will give you an idea of the overall length and structure, allowing you to properly anchor it. It will also make it easier to manage smaller parts, such as brackets and posts, which can be difficult to handle underwater.
Once you’ve assembled the frame of your floating dock on land, have someone help you move it to its final location. Depending on the size and configuration of your dock, it may be packaged on a pallet for transport or shipped in sections. Before you get to this point, be sure to test the components of the dock for durability and stability by applying weight or rocking it.
After a long winter in storage, your dock will likely need some TLC before its first summer out on the water. Begin by cleaning the surface with a gentle, environmentally friendly cleaner that won’t damage the system or the water it will spend all summer in. This is also a good time to perform regular maintenance and inspections to ensure everything’s in working order.
Before you put your dock in the water, be sure to adjust any fasteners that are loose or crooked. You can use a tape measure to get them as straight as possible and equally spaced. This will give your dock a more professional appearance and reduce the risk of accidents or failure.
Depending on your dock’s design and location, it may be anchored with concrete block anchors, chain anchors or a system of pipes that penetrate the waterbed to hold it in place. Each method has its advantages and disadvantages, but it’s important to choose a secure anchoring system that can stand up to the weather and conditions on your lake. Once you’ve chosen your anchoring system, be sure to follow the manufacturer’s instructions for proper installation.
Post-Assembly
A floating dock is a popular choice for waterfront homes. It is a durable, long-lasting alternative to stationary docks. Depending on your waterbody’s environment and location, you can choose from many different types of floating docks, including residential and commercial options. These structures have many advantages over traditional docks, including increased accessibility for boats and other watercrafts. However, constructing and installing one can be tricky. Choosing the right materials, considering the climate and waterbody’s conditions, and selecting the right construction technique are all critical to achieving a successful installation.
Before you start to install your dock, it’s important to have the necessary tools on hand. If you aren’t confident in your carpentry skills, consider hiring a professional contractor to build and install the dock for you. They will have the knowledge and experience to create a high-quality, safe dock, and they’ll be able to take into consideration your specific needs and desired features.
Once you’ve gathered the necessary tools, prepare the site for your new dock by leveling it and clearing away any debris or debris that could cause damage to the structure once installed. If you’re using a lift dock, it’s also necessary to anchor the hinge plate correctly. This will ensure that your dock tilts up and down as intended once hooked to a winch. If your section of shoreline is made of flat, unbroken rock you can drill a hole in the rock and fasten the plate to it using masonry anchor bolts. If not, you’ll need to either pour a large concrete pad (the exact size varies with dock size) or build a crib and fill it with stones to provide a solid backing for your lift dock’s hinge plate.
With the help of a friend, begin to lift your first section down into place on the lake. After a few days, if you need to, tighten the bolts holding each 300C casting and push in the black caps. You’ll want to number these in order of placement so next year you will know which ones are which.
Keep in mind that old splintery, wood dock sections can weigh 200 – 250 lbs when wet. All aluminum and vinyl docks are much lighter, and even our cedar option is much lighter than an all-wood dock.
Muck Bottoms
For seasonal boaters, spring means thawing snow and ice to make way for warmer weather and reinstallation of a dock that may have been removed at the end of last season. Getting a new or rebuilt boat dock off the ground is often a time-consuming process, but it doesn’t have to be. A few tips can ensure that your dock installation goes quickly and smoothly.
A good, quality dock isn’t just a great place to enjoy your lakefront property, but also a safe one. That’s why it’s important to use high-quality materials that are durable, functional and attractive. For instance, cedar decking is a great choice because it’s naturally rot-resistant and offers an elegant appearance. It’s also eco-friendly. If you prefer a more affordable option, pressure-treated lumber is a solid alternative (as long as your community allows it in lakes).
The type of dock you choose is also important. Permanent docks require a solid, stable underwater base. Concrete block anchors are an easy and inexpensive solution for shallow water, while EZ dock pipe and auger systems work best for areas with limited depth and firm lake bottom conditions.
Once the basic structure is in place, it’s time to finish the details. A few key additions can elevate your dock into a true oasis for family and friends to relax, play and socialize. For example, lighting is a simple way to increase visibility and safety on the dock.
Adding shade structures is another simple way to add comfort and ambiance. And finally, eco-friendly accessories like weed removal products can save you money and help prevent harmful invasive species from harming your dock or local ecosystem.
A reputable dock installer can take the guesswork out of selecting the right materials, design and equipment for your specific waterfront property. They will also have the expertise to install your new dock quickly and efficiently. They should offer a warranty on their work and be able to recommend the right types of maintenance for your dock. By hiring a pro, you can avoid costly mistakes and start enjoying your waterfront property as soon as possible this spring.
Final Inspection
Whether you live on the water or simply enjoy the beauty of it, a dock is an essential part of your waterfront property. It not only adds aesthetically value, but also provides easy access for boating and swimming activities. It is also important to make sure that your dock is safe and secure for those who use it. If you are not confident in your ability to install a new dock or boat lift on your own, it is best to hire a professional.
A reputable dock installation company will provide quality workmanship and value for your money. They will ensure that your dock is installed safely and meets all local code requirements. They will also work with you to understand your needs and help select the best dock that fits your lifestyle and budget. They will also help you with the permitting process.
The final inspection phase is a critical stage in the dock production cycle. It is when the overall product is measured against engineering, customer requirements and standards, and the final device approvals are recorded.
There are a variety of things that can go wrong during the final inspection, from framing problems to faulty wiring and improper plumbing. It is crucial that you do everything possible to prevent these issues from occurring. To avoid a costly mishap, you should ask the inspector for a list of concerns and documentation requirements, so that you can prepare accordingly.
If you are planning to have a new dock installed this spring, now is the time to start preparing. A little bit of preparation can save you a lot of time and headaches. By following the tips mentioned above, you will be able to greet your inspector with confidence and get your project off to a great start.
If you are considering a floating dock for your waterfront home, it is essential to choose the right material for your specific location. Floating docks are more versatile and customizable than their stationary counterparts, making them a good option for locations with fluctuating water levels or strong currents. Moreover, a floating dock is often easier to remove during the winter for storage or maintenance.